Increasing attention to climate issues and health and safety topics has drastically changed the types of products and services the market seeks.
Emphasising the need for decarbonisation, low emission from the machines and zero-tolerance for accidents are parameters that define the name of the game.
{alcircleadd}
In the meantime, higher productivity and increasing competition are additional key factors.
Several high-profile customers of Hencon are looking for possibilities to set up a ‘smart factory’. With Industry 4.0, cyber-physical production systems have become more wanted than ever before.
Hencon has already rolled out several AGV projects (in Europe and the USA). We believe that AGVs will be an inevitable chain in the smart industry of the future.
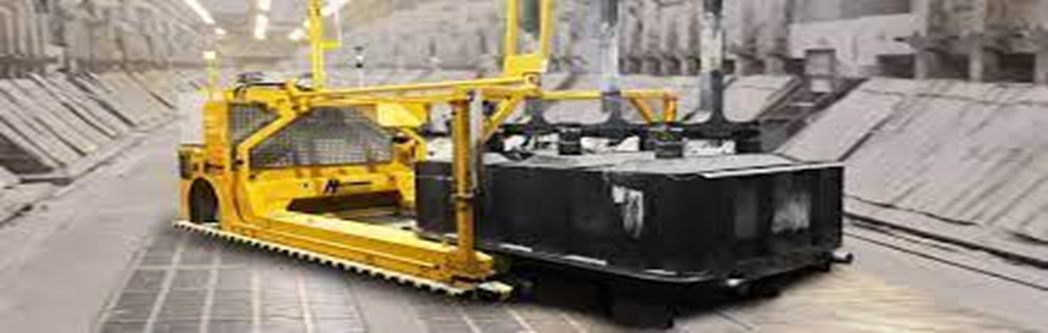
Smart Industry and AGVs
The trend towards more automated, intelligent and interconnected systems is often referred to as Smart Industry or Industry 4.0.
AGVs fit perfectly into this trend in the first place because they operate fully autonomously.
They connect to all other systems, such as the traffic management system, which in turn is connected to the plant’s Manufacturing Execution System.
An almost unlimited amount of data, such as the AGV’s live positions, battery status and readings from their scanners and sensors, can be made available for data gathering software, for example, via OPC UA.
In this way, a fleet of AGVs equipped with state-of-the-art sensors can - besides their primary task - serve as a troop of ‘explorers’, constantly collecting data on its trips through the plant, to feed a constantly updated model or visualisation of the state of the plant.
The collected information helps operators and plant managers to make better decisions based on actual and historical data. All this collected operational information is kept within the plant’s own protected network - so cyber-security is assured.
Specific challenges
Hencon wants to offer the right products, services and solutions, to get ready for those new needs and start developing Automatic Guided Vehicles.
Dust, electromagnetic fields and extreme temperatures are defining the typical frame in which AGV’s – highly precise technological machines – need to operate (in potrooms)
Another remarkable change that grew into the industry is the relationship supplier - customer. ‘In the old days’, customers ordered machines for a well-specified purpose. Nowadays there is the need for a continuous dialogue, in order to achieve goals that have never been set before.
How to prepare for automation?
What I would like to highlight in this article are the preparations that have to be taken care of before implementing AGVS in an operation.
We have experienced that automating a plant brings specific challenges. Together with our customers, we went through a steep learning curve. Basically, we learnt that it requires a proper preparation before starting implmenting AGVs in an aluminum smelter.
A few things to take care of before
- Assessment and Planning:
- Conduct a thorough assessment of the existing smelting processes to identify areas suitable for automation.
- Define specific goals and objectives for automation, considering factors such as increased efficiency, cost reduction, safety improvement, and product quality enhancement.
- Develop a detailed plan that outlines the scope, timeline, and budget for the automation project.
- Build a digital twin
- Technology Selection:
- Choose appropriate automation technologies based on the identified needs and goals. This may include programmable logic controllers (PLCs), supervisory control and data acquisition (SCADA) systems, sensors, smart cameras, robotics, and other advanced control systems.
- Consider integrating Industry 4.0 technologies, such as the Internet of Things (IoT) and data analytics, for real-time monitoring and optimisation.
- Integration with Existing Systems:
- Evaluate the compatibility of chosen automation technologies with the existing smelting infrastructure.
- Develop a strategy for integrating new automation components with the current systems to ensure seamless operation.
- Hardware and Software Installation:
- Install the necessary hardware components, such as sensors, actuators, and control devices, throughout the smelting facility.
- Implement the required software, including control algorithms, human-machine interface (HMI) software, and data analysis tools.
- Sensor Deployment and Data Collection:
- Deploy sensors to monitor key parameters such as temperature, pressure, flow rates, and other relevant variables.
- Collect and analyse data in real-time to optimise the smelting process and identify areas for improvement.
- Process Control and Optimisation:
- Implement control algorithms to automate specific tasks and optimise process parameters. This may include controlling furnace temperatures, managing material flow, and regulating energy consumption.
- Utilise feedback control mechanisms to continuously adjust and improve the smelting process based on real-time data.
- Training and Workforce Development:
- Provide training programs for the workforce to operate and maintain the automated systems.
- Develop a workforce that is proficient in troubleshooting issues related to automation and capable of adapting to the changing work environment.
- Safety Integration:
- Integrate safety protocols and systems into the automation design to ensure a secure working environment. This may include emergency shutdown systems, safety interlocks, and hazard detection systems.
- Testing and Commissioning:
- Conduct thorough testing of the automated systems to ensure functionality and reliability.
- Commission the automated smelting processes in stages, closely monitoring performance and addressing any issues that arise.
- Continuous Monitoring and Maintenance:
- Implement a robust maintenance plan to ensure the ongoing reliability of automated systems.
- Establish continuous monitoring mechanisms to detect abnormalities, prevent downtime, and optimise performance.
- Iterative Improvement:
- Regularly review and analyse performance data to identify opportunities for further optimisation and improvement.
- Implement iterative changes and updates to the automation system based on lessons learned and advancements in technology.
In this complete process, Hencon will involve and guide the customer through the process. The time to implement AGVs in an operation is estimated at least double the time of the purchase of traditional vehicles.
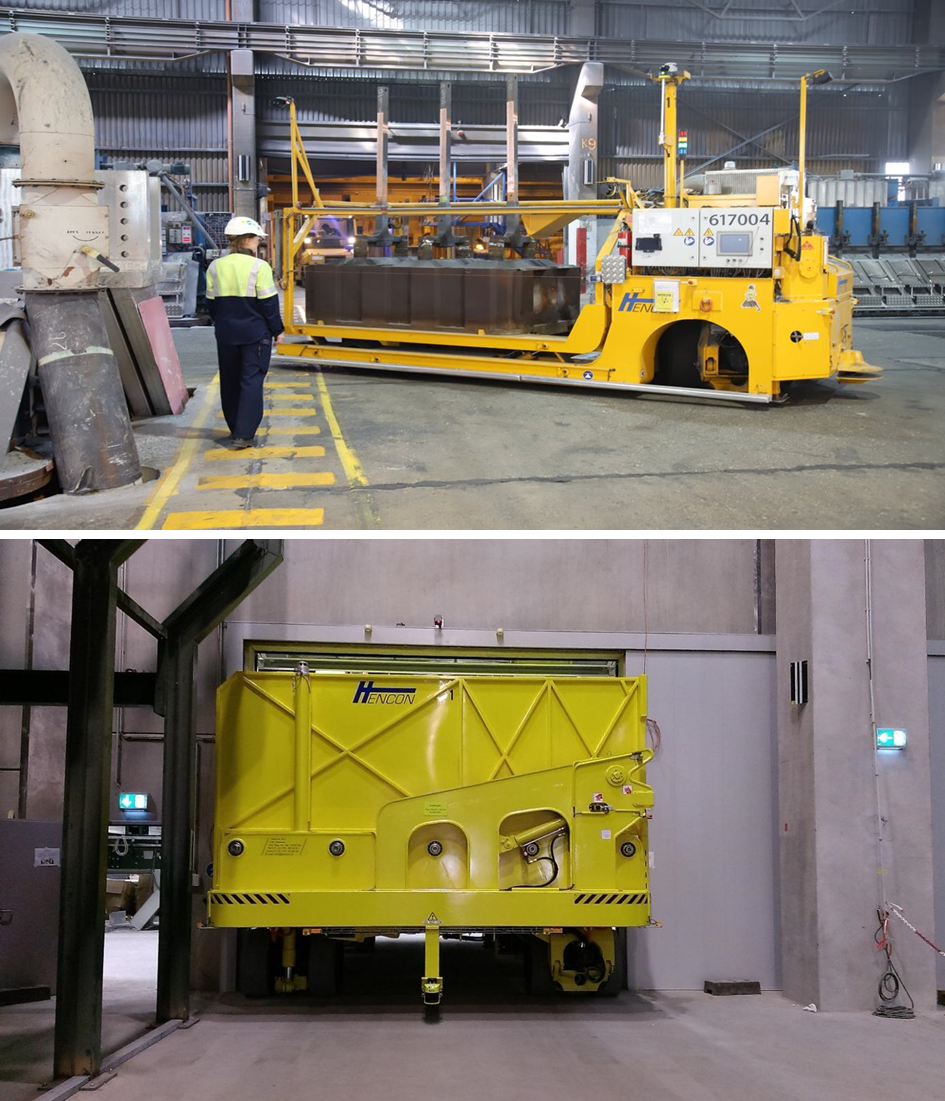
Overview: Benefits of AGV’s
AGVs will contribute to the efficiency of all kinds of production processes and all kinds of logistical processes while increasing safety and reducing costs. The following benefits and properties can be identified:
- Suitable for picking up, transporting and unloading any load (fluid aluminium, anodes,…)
- Electrifying the powerpack leads to zero emission and less noise
- Low costs (maintenance costs are extremely low, personnel costs are reduced tremendously) and a much higher output
- 100% Safety (no personnel involved)
- Constant communication between machine and supervisors
- System helps to track & trace quantities and locations of the transported materials
- Remote and even off-site monitoring of operation
- Remote OEM support
- The AGV will be directed via a Supervision system to the specific locations that are indicated by the Manufacturing Execution System (MES). This guarantees that the AGV is always at the right time at the right place and ensures the best production efficiency
- Machine works 24/7 with an unprecedented reliability
- More compact machines (no cabin required, no combustion engine)
- Complying with specific needs of Industry 4.0
- A beneficial collateral effect of AGVs is that an AGV moves in a much more predictable and controlled way than a human-operated vehicle (e.g. it doesn’t bump into its load when picking this up).
This, in combination with the lack of an operator’s cabin, electric engine, etc., results in a much lighter construction than conventional vehicles.
Thanks to this, impressive energy consumption can be achieved and floor loads are lighter as well, allowing further maximisation of transport capacity of transport vehicles within the same floor load limitations, by pushing the vehicle/cargo weight ratio further.
Because our AGVs are much more compact than traditional machines, they are also able to enter areas with limited width/height - where a human driven vehicle would be too large.
If you’d like to know if/how AGVs can be applied in your industry, Hencon is always available for more detailed information. Appointments can be made at the customer’s offices or at Hencon’s.